Project Example: AWP Profile optimisation
Optimisation of symmetrical blade profiles for a wind turbine with vertical axis
In this project, thick, symmetrical airfoils for a vertical wind turbine were optimised and tested in the wind tunnel. The software tool used was ADflow and an optimiser that uses a gradient-based optimisation strategy. An important aspect especially of the wind tunnel tests was to determine the influence of the surface roughness. In practice, windmill blades get a rough surface in the front area due to insects. This has a great influence on the effectiveness of the airfoil. The roughness was taken into account in a second optimisation pass in the CFD simulations. The optimiser now tries to achieve the smallest possible area where the boundary layer detaches. The calculated results and the results measured in the wind tunnel agreed better.
Vertical Wind Turbines
The Swiss company Agile Wind Power (AWP) develops, builds, and sells vertical wind turbines. Such wind turbines are quieter than conventional ones. Based on the experience with the first generation of wind turbines, an inflow-optimised blade pitch was developed, which promises better efficiency. In addition, aerodynamically better profiles are being developed in this project. Symmetrical profiles are being considered for this because they should be as torque-free as possible.
Two-stage approach
In the first development step, wing profiles are examined with numerical methods and the results are compared with wind tunnel tests. With these results, a second optimisation cycle was carried out and the best wing profiles were tested in the wind tunnel.
Optimisation parameters and tools
For energy generation, the best possible ratio of wing lift to drag should be aimed for. This is found in the thick airfoils used with relatively large angles of attack of the airfoil to the local airflow. In addition, attention must be paid to the position of the aerodynamic centre and to the maximum angle of attack at which the flow breaks off. An essential point of the investigations was the influence of the surface roughness. The influence of the thickness of the profile's trailing edge was also taken into account.
ADflow was used as the current simulation tool on the SoE cluster, and openMDAO as the optimisation tool.
Wind tunnel tests
Two measurement campaigns were carried out in the subsonic wind tunnel of the ETH Zurich. The wings were installed vertically in the wind tunnel over the entire height. The forces and moments were measured on the ground. In addition, drag measurements were made in the wake with hot wire probes. The wind tunnel models were CNC milled from polymers. The fouling conditions were simulated by sandpaper with grain sizes from 150 to 220 to simulate erosion and fouling by insects, oil, sea salt. The measurements were carried out for angles of attack up to 30°.
Optimisation results
The thickness and symmetry specifications limited the optimisation process. The pressure gradients on the suction side. As is known from four-digit NACA airfoils, even the smallest disturbances lead to detachment at low inflow velocities. The optimiser calculated the best lift to drag ratio at an angle of attack close to the separation limit. Now a more harmless breakaway behaviour was also required. The optimiser thickened the trailing edge so that lower gradients occur in the suction area, but greater dead water behind the thicker trailing edge.
In the second optimisation phase, the surface roughness was included. The robustness of the profile with regard to the breakaway behaviour was achieved by a slightly lower aerodynamic quality.
The wind tunnel tests confirmed the expected performance data and the desired breakaway behaviour even with a dirty profile.
Results
The simulation tools used proved to be powerful tools. The influence of the surface roughness is a great challenge. The decisive physical parameters are the profile thickness and the comparatively low inflow velocity. The results of the optimisation with a rough profile show a tendency towards profile geometries with a thicker trailing edge.
The project was funded by the Swiss Innosuisse.
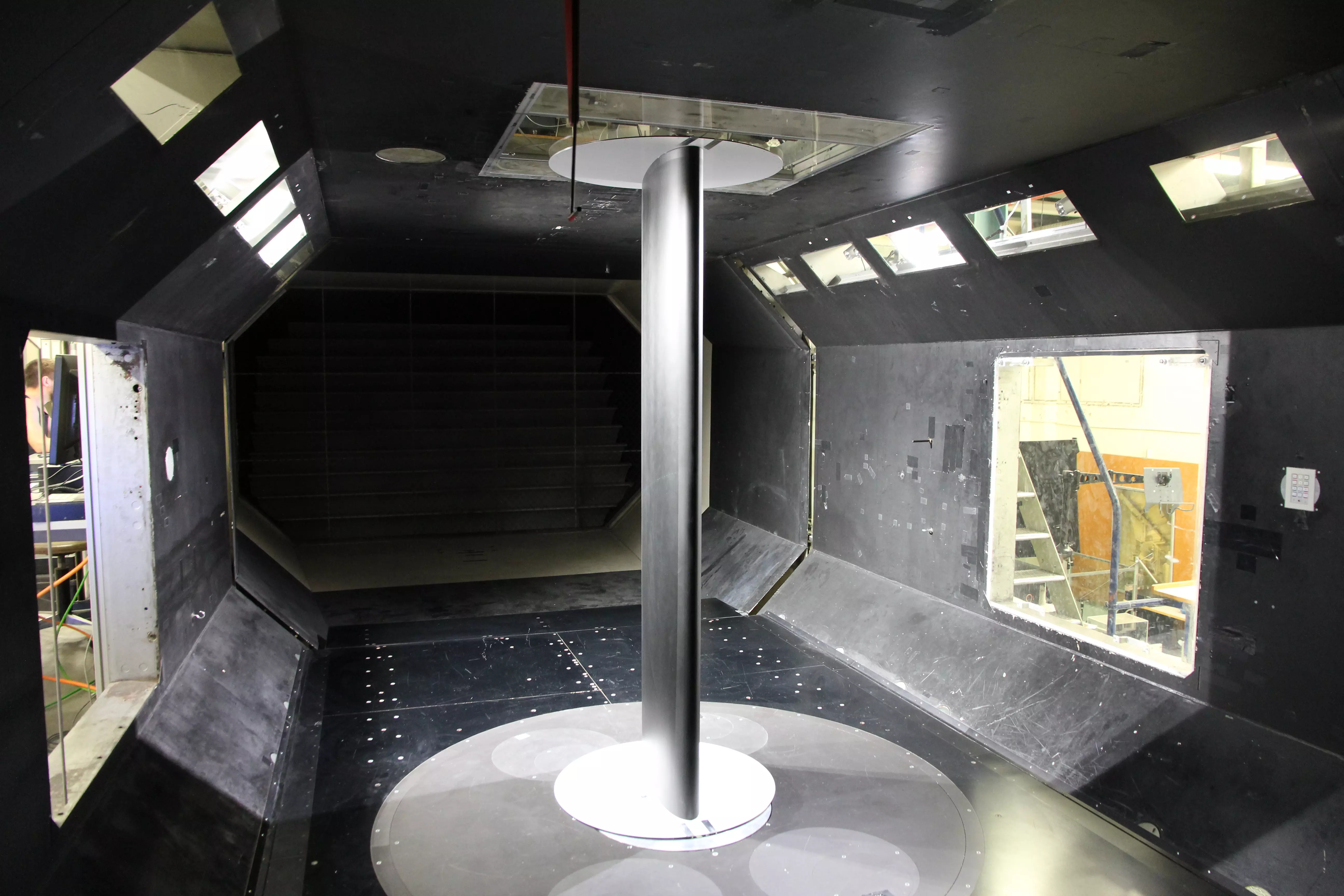
At a glance
Participating institutes and centers:
Project Partner: AGILE Wind Power AG
Financial contribution: The project was funded by the Swiss Innosuisse
Project status: completed