Example project: Computational models for heat exchangers
Computational models developed for heat exchangers used in settings involving high dust exposure
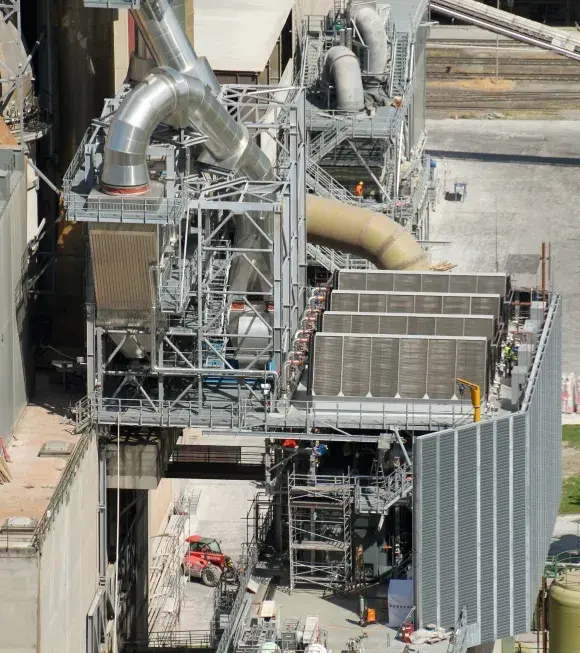
In industry, large amounts of waste heat are produced in the form of highly dust-laden gas flows. Recovering this energy places high demands on heat exchanger systems. Dust accumulates on the heat transfer surface, acting as an insulating layer which greatly reduces the amount of heat transferred. This is referred to as fouling. In an effort to protect against the consequences of fouling, heat exchangers are equipped with a more expansive transfer surface, which leads to higher investment costs. In this project, the preheater heat exchanger of the ORC system (ABB) at the cement plant in Untervaz (Holcim) is analysed with regard to fouling.
Implementation and results
The preheater heat exchanger in Untervaz, recovers about 10 MW of heat energy from the highly dust-laden (approx. 100 g/Nm3) exhaust gas. The impact of dust deposits on the transfer of heat is crucial in this process (see Fig. 2). With the help of thermodynamic models, the influence of fouling on the overall heat transfer coefficient, or k value, has been examined.
The models have been validated with measurement data, taking into account a homogeneous dust layer on the heat transfer tubes. Validation was performed by comparing the modelled and measured substance flow outlet temperatures as well as thermal output. Comparisons showed a close correspondence between the models and the measurements with relative deviations of 2 %. The resulting k value is lower than what was anticipated during construction of the system (see Fig.3).
At a glance
Institutes and centres involved:
Project partners:
Project status:
completed
Contact:
ZHAW School of Engineering, Lecturer in Measurement, Control and Regulation Technology, Prof. Dr. Walter Siegl, phone: +41 (0) 58 934 75 34, e-mail walter.siegl@zhaw.ch