When turbines inadvertently let off steam
The Institute of Energy Systems and Fluid Engineering has collaborated with General Electric on a project to optimise steam turbines. When examining the sealing technology of these plants, the researchers came to an astonishing result.
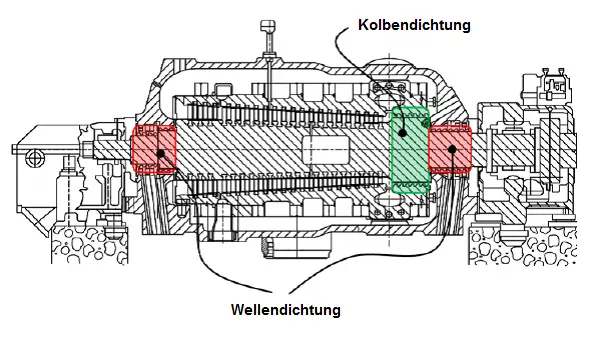
Steam turbines play an important role in energy production today in both solar thermal power plants and in the use of fossil fuels. At the same time, the electricity market is becoming more vociferous in its call for more efficient turbines “To achieve this, however, we need to have a better understanding of the machine components”, explains Martin König. A research assistant at the Institute of Energy Systems and Fluid Engineering (IEFE), König has worked with Peter Stein from General Electric on gaining a more precise understanding of the technology and, on this basis, to find ways of optimising it. In doing this, they focussed on the steam turbine seals.
Unknown steam loss
Steam turbines are used to transform heat into electric energy using steam. The performance and safety of the plants depends heavily on the seals that are used. These seals are located between the rotating and stationary parts of a turbine and influence the flow of steam. This gives rise to a typical problematic situation: “Some of the steam doesn’t flow over the turbine shaft as intended but escapes into other areas. This makes the machine inefficient”. How much steam is lost through the various pathways in the sealing system has not been established so far and has merely been estimated. König adds: “This is exactly what we wanted to investigate.”
Tests on a 900 megawatt turbine seal
In order to carry out their investigations, the researchers needed a realistic test plant. “But until now nobody wanted to sacrifice a steam turbine for testing purposes.” Luckily, however, General Electric provided the components of a 900 megawatt turbine. Using air instead of steam, the researchers were able to measure and record leakage in the affected parts of the sealing system over the period on one year. “The plant components provided by our project partner allowed us to carry out tests in realistic conditions and achieve very precise results.”
Realistic results
After completing the measurements, König and Stein came to an astonishing result: twelve per cent of the leakage is caused by misdirection of the steam within the sealing system. “That’s a big difference from the almost 50 per cent that was previously assumed.” König is currently presenting this result at the American Society of Mechanical Engineers TURBO EXPO in North Carolina. But, for König, another achievement is just as important as the test result: “We were able to develop a testbed that provides realistic results, which is the basis for optimising the seals. This has brought us a big step forward in gaining a better understanding of the technology and thus in being able to improve the efficiency of steam turbines.”