Greater precision in the additive manufacturing of metal parts
The FDM (fused deposition modelling) 3D printer, with which it is very easy to produce components from plastic filaments, is probably the best-known 3D printer for additive manufacturing. While plastic is relatively simple to process, the additive manufacturing of metal parts on the basis of “selective laser melting” is far more demanding. Within the framework of this project thesis at the Centre for Product and Process Development (ZPP), solutions were sought to further improve machines for selective laser melting.
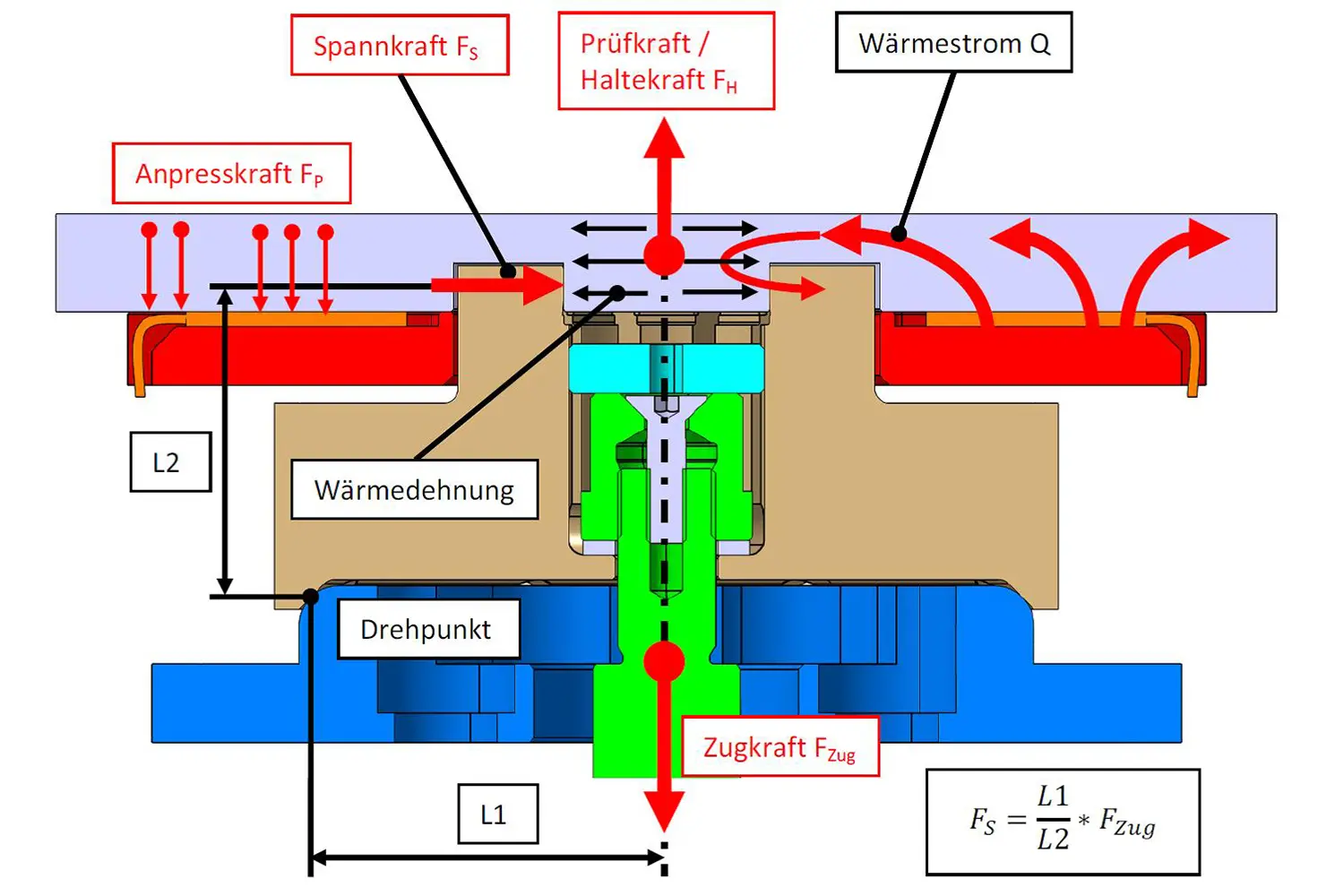
A workpiece created without any tools
Thanks to the selective laser melting (SLM) manufacturing process, it is possible to produce complex components and structures such as cavities, undercuts and lightweight structures in metal directly from the CAD model on an additive basis. Using SLM, metal powder is applied to a worktop in a very thin layer and melted using a laser where the layer information from the CAD model is located. When the melting process is completed, a new layer of powder is applied and fused to the existing layer, again using a laser. The desired object is thus created layer by layer. The entire procedure resembles a welding process at temperatures that in some cases exceed 1,500°C. Since the surfaces of the SLM-manufactured components are relatively rough, they often have to be finished subsequently, for example on a machining centre or a milling machine.
Thermal expansion causes high stresses
A very high level of thermal energy is introduced by the laser at certain points. This leads to internal stresses in the components due to the large temperature gradients that occur during the process. This should be prevented by pre-heating the working area. Furthermore, it is not possible at present to accurately position a building panel in the laser melting system in order to subsequently finish machining the SLM-produced parts in a milling machine exactly without reclamping errors arising. A zero-point clamping system aims to simplify this.
Working space with heating panel and zero-point clamping system
Within the framework of this project, a system was developed that is able to precisely position, clamp and heat a building panel. Weak points were identified by means of construction FME analyses and then checked with FEM simulations and subsequently optimised. With the system that was developed, positioning is carried out via a centring element with play, while clamping is performed with pneumatically operated clamps. The heating system is based on heating cartridges and temperature sensors to heat the building panel up to 300°C. The heating system serves to eliminate internal stresses in the SLM components. Subsequent integration into the SLM system is possible. The zero-point clamping system developed makes it possible for the final machining of SLM components to be performed on the 5-axis NC milling machine available at the ZPP.
About the author of the thesis
The project thesis entitled “Development and construction of the working area of an additive manufacturing system (laser melting machine)” was written by Sandro Brunner within the framework of his Master of Science in Engineering (MSE). He was supervised at the Centre for Product and Process Development in the focus area of Advanced Production Technologies.
Supervisor: Andreas Kirchheim