Fluid Engineering increases the efficiency of Cotton cleaning equipment
Initial conditions and goals
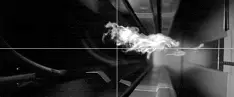
Raw cotton is used as a base material and spun into yarn.
The supplied cotton contains various foreign substances, which negatively impact the quality of the finished product. For this reason, the cotton undergoes various cleaning levels at the beginning of the spinning process, in which the system provided by Jossi Systems AG is used as the final level. In this facility, uncleaned cotton tufts are fed through a transport duct using airflows. Inside this duct, a variety of sensors detects contaminants in the cotton and ejects them using compressed air impulses. Although it was possible to detect almost all types of foreign matter, not all contaminants were ejected. The goal of this project was the ejection of all foreign matter detected by the system.
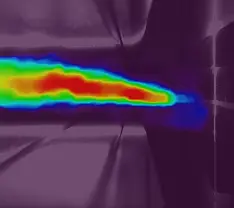
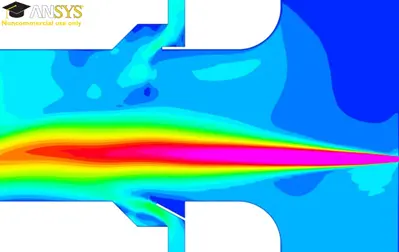
Implementation and results
In the first half of the project, the airflow conditions in the ejection module were investigated both experimentally, as well as through numeric airflow simulations. These results led to redesigning several components of the ejection module, which were developed, produced, and tested. The flow optimisation resulted in a significant improvement of the ejection rate compared to the existing module.
At one glance
Involved Institutes and centers:
Project parter:
- Jossi Systems AG
Co-financing:
- Innosuisse (former KTI)
Project Status: completed
Project details
Download Project Flyer: Efficiency of Cotton cleaning equipment(PDF 342,3 KB)