Polymeric Coatings
The laboratory of polymer coatings offers the development of coatings by means of wet chemical processes. The spectrum ranges from monomolecular layers to paint chemistry.
The main focus of the research group is the development and formulation of functional coatings. New functions can be implemented directly on surfaces by means of grafting processes, or by means of a functional (lacquer) coating. The coating materials are developed for a processability in industrial processes. The most important coating processes can be simulated and the coating materials can be adapted accordingly. For this purpose, extensive analytics and a extensive coating technology are available.
Formulation of functional polymer coatings
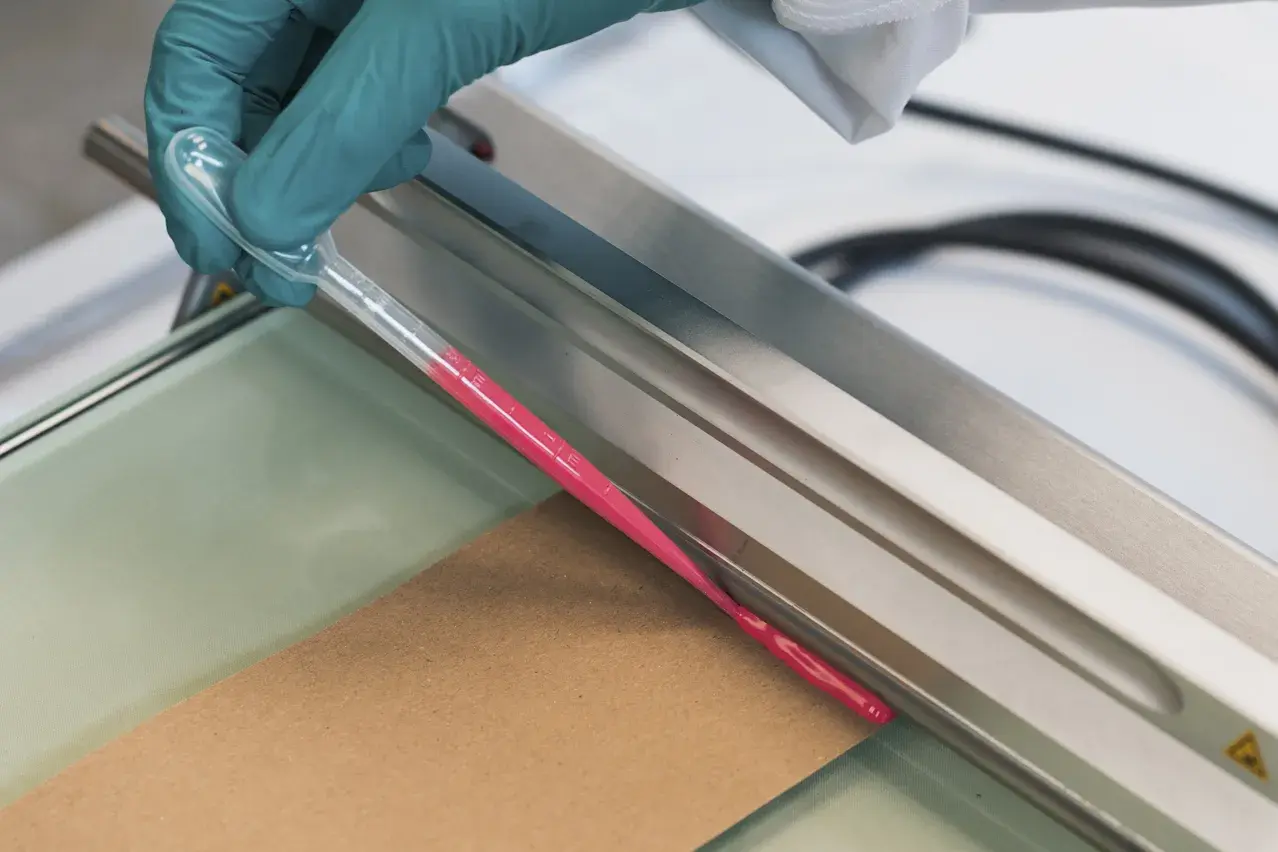
The Laboratory for Polymer Coatings has many years of expertise in the development, formulation, application and characterisation of functional coatings that are deposited from the liquid phase. Chemists, material scientists and engineers work hand in hand in our laboratories and solve the many problems that can arise during development in a pragmatic manner.
Our industrial customers include companies from the packaging, converting and machinery industries as well as the medical technology sector. Our coatings can be found in trucks, but also in luxury watches or are used in heart examinations.
We develop coating systems, sol-gel coatings or nanocoatings that introduce a specific function into the product. Typical functions include hydrophilicity, hydrophobicity, sliding friction, adhesion to various substrates, biocidal surfaces, sound-absorbing surfaces, defined barrier properties such as water vapour barriers or oxygen barriers, embedding of functional molecules such as fluorophores for sensor technology and many more.
We utilise our knowledge of chemical synthesis, the modification of polymers, the processing of binders and resins as well as coating technology. New functional molecules are created in our laboratories, commercially available binders are used and chemically modified or coatings with new properties are created from commercial products through skilful formulation.
We have all the methods of organic synthesis and coating technology at our disposal. Whether reaction flasks and automatic chromatography systems, NMR or GPC, bead or basket mills, ovens or UV lamps for cross-linking or the determination and adjustment of viscosity, we are ideally equipped for new challenges from our industrial partners. Comprehensive analytical methods for both liquid and cured coatings help us to develop in a targeted manner.
We emphasise the use of raw materials from natural sources, in particular from waste streams, and we are happy to develop these into a functional coating that is only slightly or not at all behind those from petrochemical sources.
The substrates we coat include flexible materials such as paper or plastics, but we also use metals, glass and wood. We are not afraid of "difficult" substrates such as polypropylene either, as we are currently in the process of developing a promising primer system for it.
Application technology
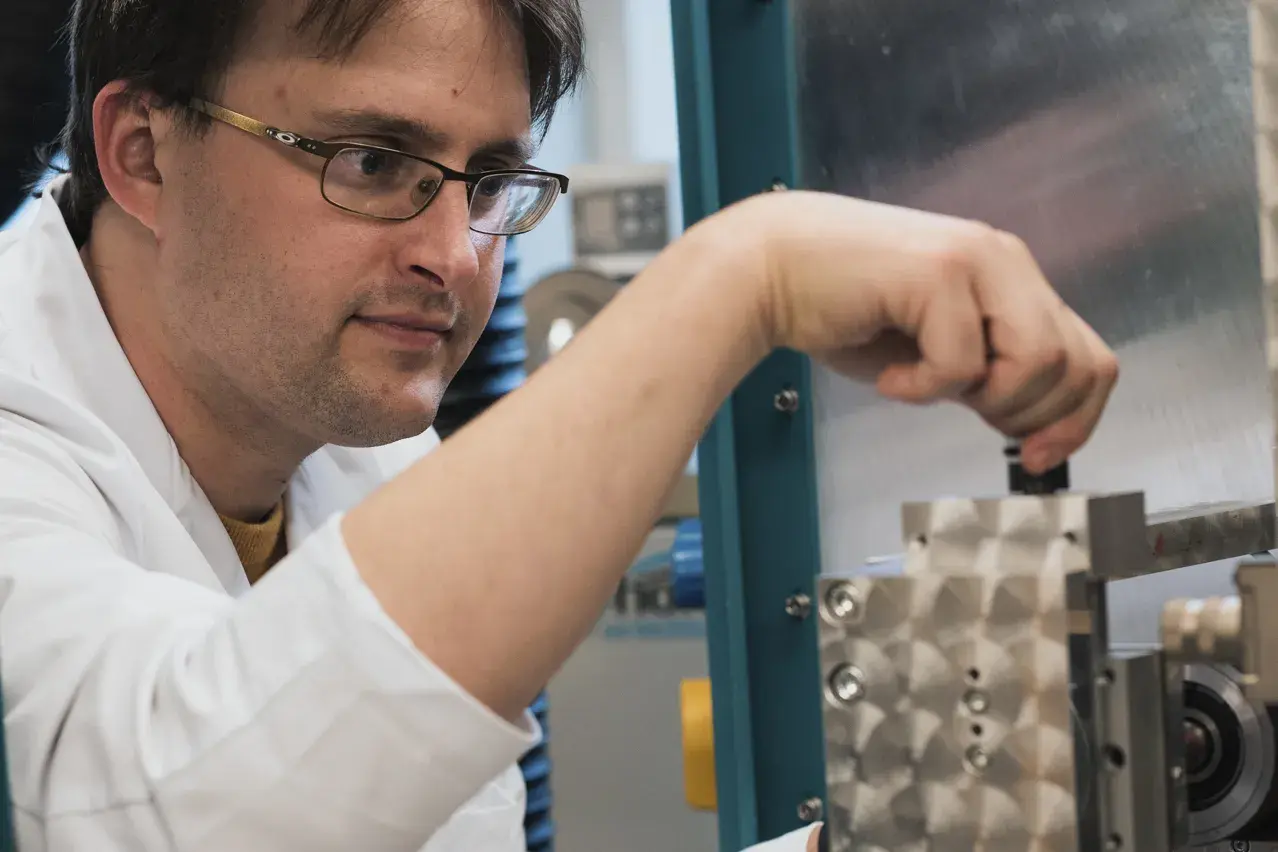
The formulation of a coating compound is only one important component for transforming a coating into a functioning product. The type of the application process is just as important. We are very aware of the interplay between formulation and application method, which is why we either adapt our coating formulations to the given application process or suggest what we consider to be the best application method for a given coating problem.
We have access to the most important coating methods on a laboratory scale and in most cases also on a pilot plant scale.
In addition to typical laboratory methods such as doctor blade coating, spin coating or dip coating, we also use "large-scale" processes such as spraying (wet and powder), foulard, slot die, roller and air doctor blade, (roller) screen printing or flexographic printing. For flexible materials in particular, we have invested in a fully equipped roll-to-roll coating system equipped with all these coating methods as well as with an air circulation dryer, IR dryer and UV curing unit. This allows coating problems to be recognised at an early stage before extensive tests are carried out by the industrial partner.
Our table-top coating system with high-precision slot die and flexographic printing (can be expanded to include other coating and printing processes) can be used for the production of high-precision coatings, such as for solar cells, even with small quantities of expensive coating solutions.
In the laboratory, we try to develop as close as possible to the final coating method in the early stages of development. For example, we can simulate the drying conditions of a continuous oven in the laboratory using a drawer dryer.
Characterisation of coatings
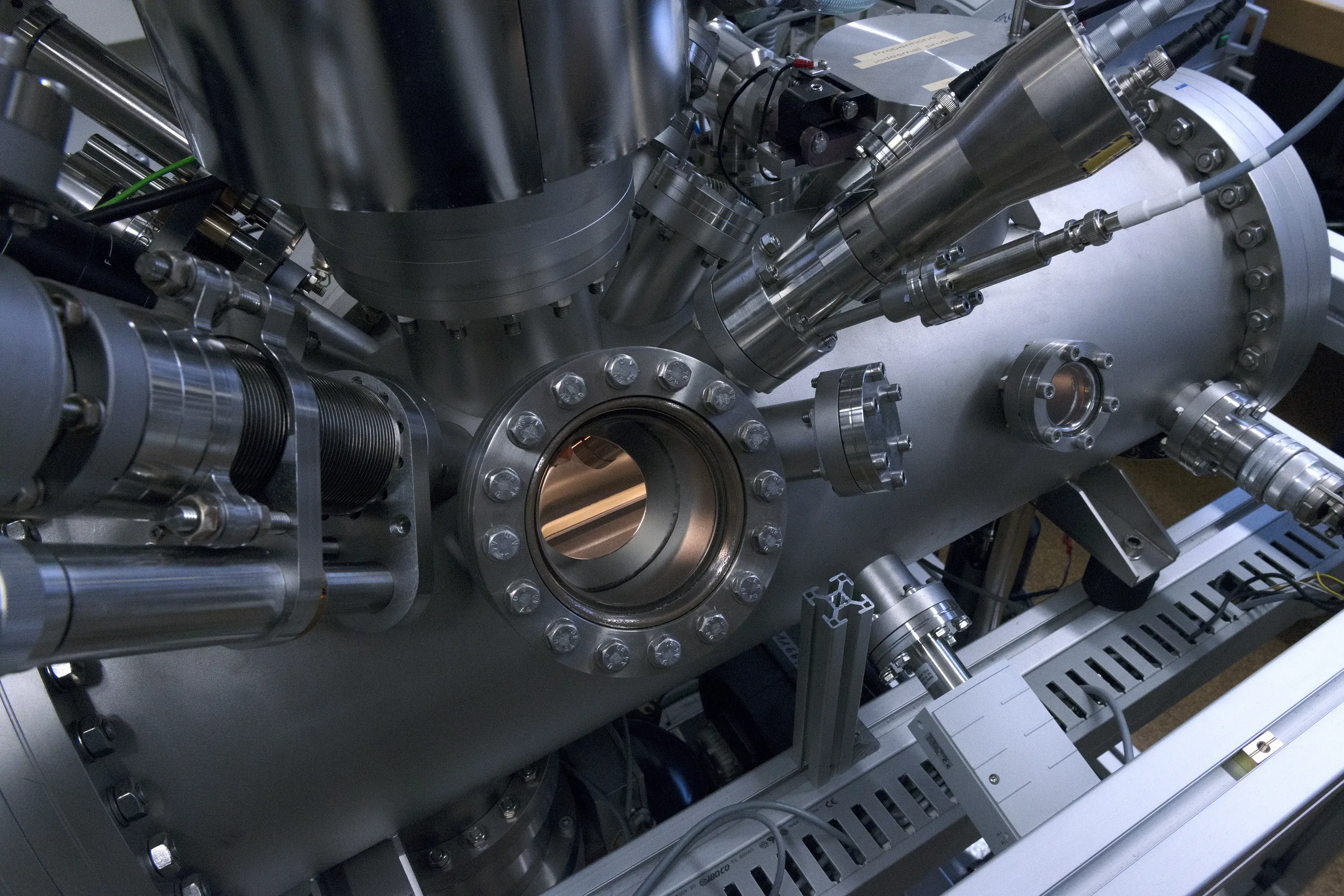
The development of a coating is impossible without the associated analysis. We have numerous analytical methods at our disposal for analysis of both the coating compound and the cured coating. We also have access to the entire IMPE machine park and the other analytical facilities of the ZHAW (especially in Wädenswil).
For the development of a coating compound we mainly use:
Benchtop NMR: for reaction control and identification of organic compounds; rheometers to determine viscosity; laser diffraction and dynamic light scattering to determine particle sizes; GPC to determine molecular masses of polymers
The following methods are primarily used to determine cured coatings:
DSC / TGA, also coupled with MS or IR; IR-ATR; optical microscopy, SEM-EDX; XPS (Fig. 3); contact angle (static / dynamic / roll-off angle).
Analyses of defects are possible with IR and Raman microscopy and the optical appearance can also be characterised by UV-Vis spectroscopy and colourimetry (angle dependent or in the integrating sphere).
You can find an overview of the IMPE's entire analytical machinery on our information sheet.