Structural Integrity and Aircraft Repairs
"Besides its fundamental significance in aeronautics, Aerodynamics plays an important role in different technical disciplines."
Prof. Dr. Leonardo Manfriani, Team Leader Aerodynamics
Field of Expertise
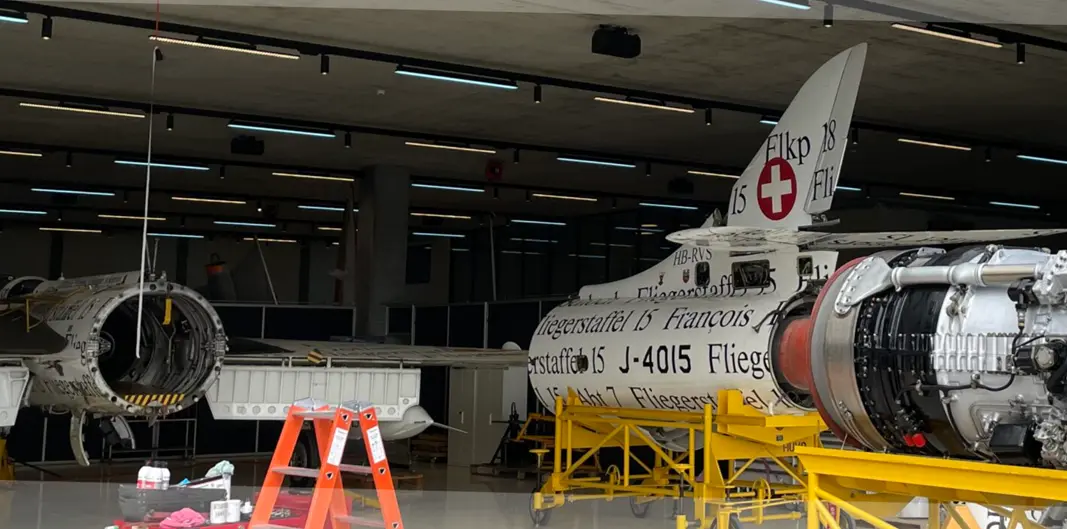
Structural integrity plays a particularly important role in the implementation of modern manufacturing processes and in the use of hybrid structures. It significantly influences the design of new aircraft, as the structural integrity must be ensured over the entire service life of the aircraft. The aerodynamics team has expertise in aerodynamic analysis, design, measurement and testing, computational fluid dynamics (CFD), flight test techniques and certification of aircraft for flight performance and flight characteristics.
Within the scope of projects, which are often combined with Bachelor or MSE Master theses, the following topics are dealt with in depth:
- Development of maintenance and inspection concepts to ensure structural integrity
- Load calculations for fatigue load cases and fluid structure couplings
- Analysis of cracks from operational damage, development of additional inspections and repairs
- Execution of Structural Risk Assessments to achieve the economic service life
- Analysis of structural integrity (identification of fracture and maintenance critical parts)
- Structural Risk Assessment / Development of Supplemental Structural Inspection Document for Ageing Airplanes
- Fatigue Analysis of the Hawker Hunter’s MK58/68 Leading Edge Spigot Structure
- Analysis of the structural integrity of the Venom DH112 in civilian use
- Development of an inspection concept for the vampire DH110 and DH115 for civil use
Various methods and procedures are used, such as:
- Load calculations with tools like FLOW5, ANSYS CFX or FLUENT
- Structural analysis using FEM
- Crack initiation calculations using CITime
- Crack growth calculations using AFGROW
There is also an intensive cooperation with the Flieger- und Fahrzeugmuseum Altenrhein (FFA Museum - Fliegermuseum Fahrzeugmuseum Altenrhein) and the Jet Prop Heritage in Altenrhein to ensure the structural integrity of the former Swiss Air Force jets.
- Consultancy in the areas of aerodynamic layout and development of aircraft
- Planning, execution and evaluation of wind tunnel tests in various aerodynamic fields, including aircraft, propellers, wind turbines and vehicles
- Planning, execution and evaluation of flight tests: measurement of flight performance, evaluation of flight qualities and certification tests
- Experimental and numerical characterisation of wind turbines
- MEMS Equipment: The MEMS equipment is used for acceleration and strain measurements on structural components. We have a mini data logger MSR 160 for strain gauge measurements (weight 80g) and a mini data logger MSR 165 for shock and vibration measurements (3-axis accelerometer incl. atmospheric pressure, weight 69g).
- Wind tunnel ALFA: With the ALFA wind tunnel it is possible to perform reliable aerodynamic measurements thanks to its modern measurement systems and excellent flow quality.
- RECREATE: A revolutionary concept for efficient long range flight. EU-FP7 project in collaboration with several European universities and research centres.
- Hybrid cooling of a high performance electric propulsion system for aircraft
- Design of Winglets for the DG300 glider
- Research on drag reduction through riblets
- Wind tunnel tests and optimisation for the rotor blades for the Wepfer wind turbine
- Concept for static structural test on a helicopter
- Fatigue analysis for the preparation of Supplemental Structural Inspection Documents SSID for ageing airplanes
- Development of engine repairs on non-rotating engines of the types CFM56 and PW4000
- Consulting for dimensioning of structural components under varying loads
- Execution of simple measurements (strains) on components with MEMS sensors