Lightweight construction of a die-casting mould with the help of topology optimisation
Working in cooperation with Bühler AG from Uzwil, Switzerland, and on the basis of an existing die-casting mould design, analysis was carried out to determine how a weight-optimised design could be developed using topology optimisation methods, and to what extent this would be economically viable.
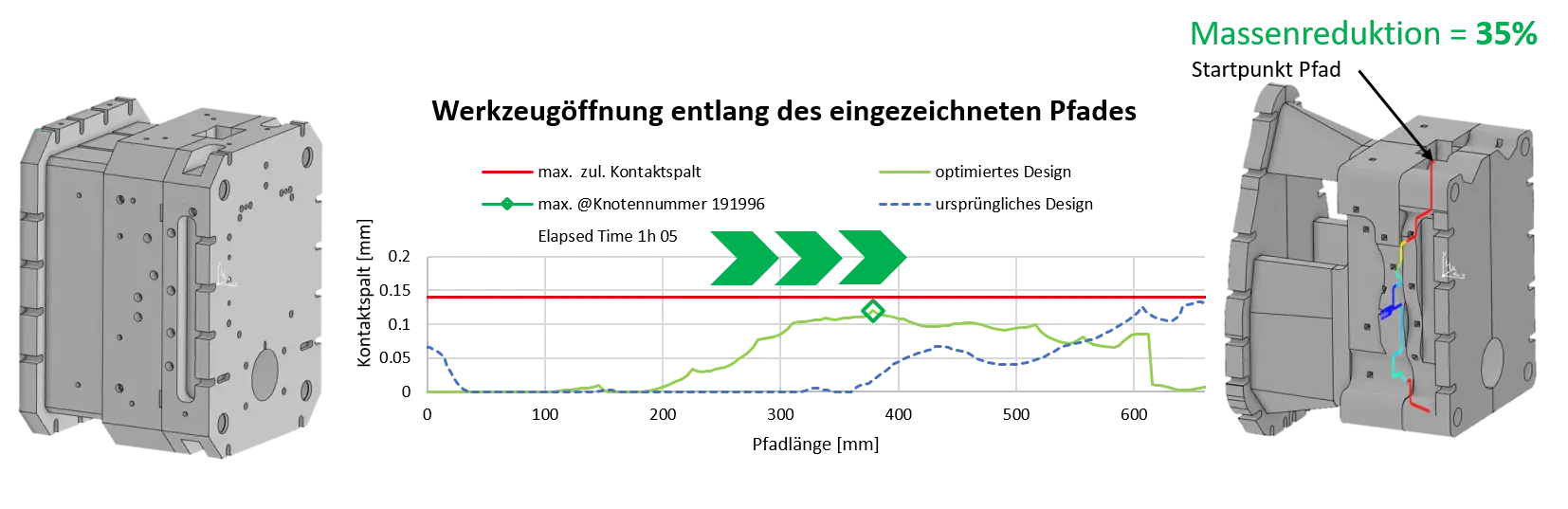
In a preceding project (EVA), the necessary bases in the field of topology optimisation and die casting were created and the mould design to be investigated was analysed and documented. With the aim of reducing weight and thus the material costs of the mould, a thermomechanical, strongly coupled topology optimisation was conducted on the mould frame and an optimised design was developed in work for this project thesis (VT). Finally, on the basis of a comparison between the original and the optimised design, it was possible to demonstrate the potential of a topology-optimised die-casting mould and to categorise the development expenses.
The original geometry and the loads occurring were analysed in a reference calculation. Knowledge in the area of thermomechanical structural optimisation was expanded gradually using simplified models in order, finally, to perform a thermomechanically strongly coupled optimisation of the mould frame. On the basis of fairly simple geometry, it was then possible to demonstrate further approaches to thermomechanical optimisation.
In this project thesis, it was shown that, with the applied methods, a mass reduction of 35% can be achieved as regards the reference geometry with a similar level of stiffness. General guidelines for the design of the mould frame were derived from the acquired data. The methods developed were described and reference was made to the challenges and possible extensions of the applied methods. It was shown that thermal loads must be taken into account in the structural optimisation so that an appropriate solution can be found. The occurrence of thermal and mechanical loads in a component is frequent in technology. Further developments in the field of structural optimisation software for thermomechanical problems are thus to be expected in the near future, as are associated improvements in the performance of the relevant optimisation.
About the author of the thesis
The project thesis entitled “Lightweight construction of a die-casting mould with the help of topology optimisation” was written by Sandro Mares within the framework of his Master of Science in Engineering (MSE). He was supervised at the Centre for Product and Process Development in the focus area of Advanced Production Technologies.
Supervisor: Anton Höller
Fachartikel Swiss Engineering, September 2020(PDF 2,5 MB)