Project example: Wind Tunnel
The ZHAW School of Engineering required a wind tunnel for research and training purposes. However, there were no ideal ready-made solutions available on the market, so researchers and students worked together for two years to develop their own wind tunnel – from concept through to commissioning.
Wind tunnels are particularly valuable in the aerospace industry. They enable wind-current phenomena and forces to be investigated on the ground under controlled conditions. Future aerospace engineers who are studying at the Centre for Aviation (ZAV) at the ZHAW School of Engineering now also have the opportunity to be actively involved in research using the school’s own wind tunnel with a Göttingen-type design.
“What is unique about this is that we were able to realise the devel-opment from A to Z completely in-house. With its 13 institutes and centres, the School of Engineering has such a broad base that we had access to all of the necessary expertise internally.”
Prof Dr Leonardo Manfriani, project head, Centre for Aviation (ZAV)
All of the expertise available internally
The initiative for a wind tunnel was provided by Prof Leonardo Manfriani, who as a lecturer in Aerodynamics and Flight Engineering supervised various project and Bachelor’s theses on the topic. Approximately two years were needed to get from conceptualisation to commissioning. “What is unique about this is that we were able to realise the development from A to Z completely in-house,” Manfriani explains. With its 13 institutes and centres, the School of Engineering has such a broad base that we had access to all of the necessary expertise internally.” In addition to aerodynamic know-how from the ZAV, the Institute of Embedded Systems (InES) was responsible for the software and the Centre for Product and Process Development (ZPP) was in charge of planning the construction. Numerous students also assisted the institutes with the development of the wind tunnel by means of their project and Bachelor’s theses. Bühler AG in Uzwil was ultimately contracted for the mechanical manufacturing.
Controlled laboratory conditions
The possible uses for the wind tunnel are very diverse. In addition to being used for training purposes in Aviation, Mechanical Engineering and Energy Engineering, the wind tunnel can be hired by third parties, which the ZAV hopes will lead to concrete research contracts. “An entire aircraft may not fit in our wind tunnel but we can test the aerodynamic qualities of objects under precisely controlled laboratory conditions,” Dr Michel Guillaume, head of the ZAV, explains. “For example, we can work on rotor-blade optimisation for wind turbines or test and improve the aerodynamics of products such as motorcycle helmets.” The test models are subjected to air current speeds of up to 50m/s (180km/h).
“An entire aircraft may not fit in our wind tunnel but we can test the aerodynamic qualities of objects under precisely controlled laboratory conditions.”
Dr Michel Guillaume, head of the Centre for Aviation (ZAV)
Special construction
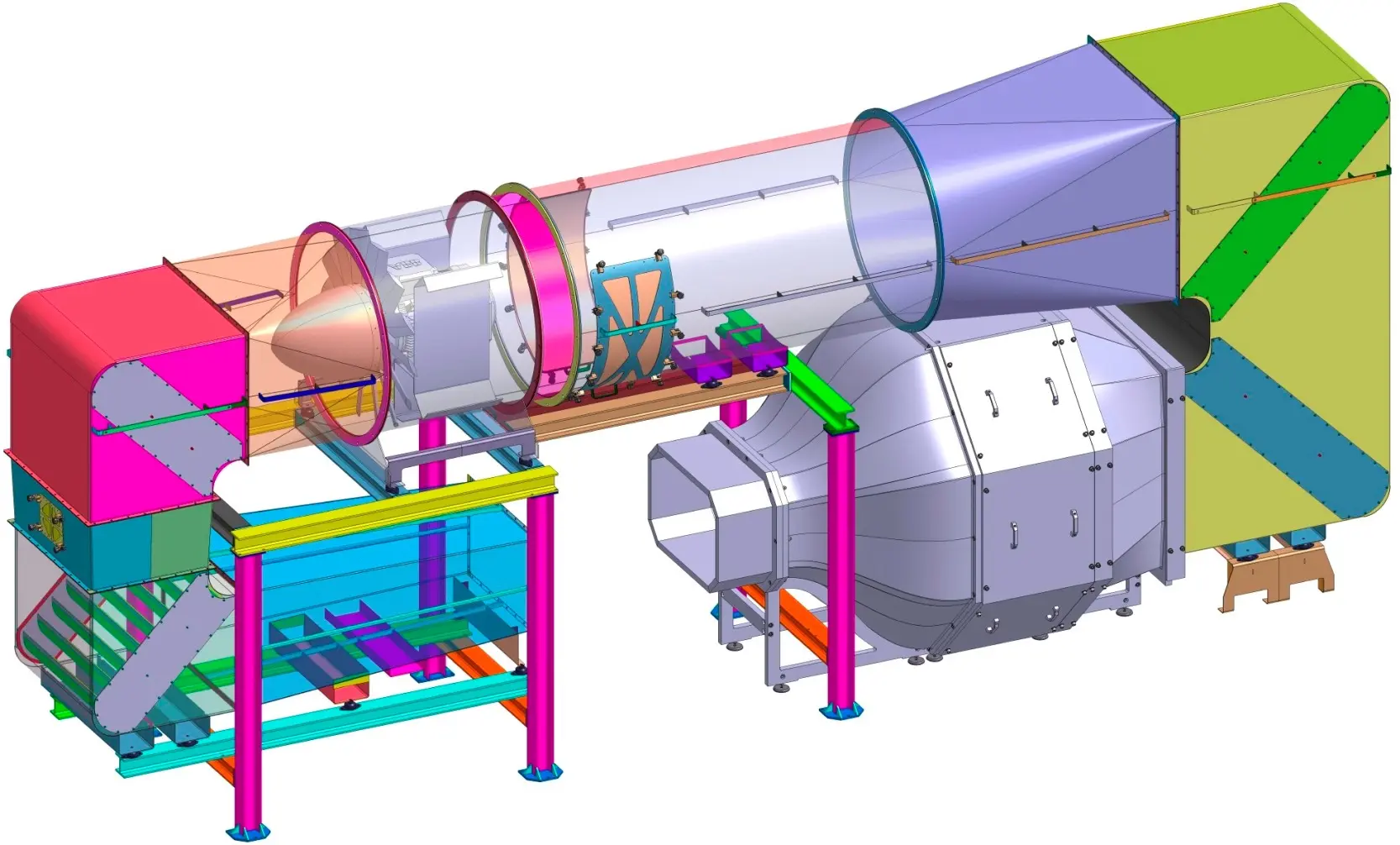
The wind tunnel is constructed mainly of stainless steel panels. The most sensitive parts in aerodynamic terms directly in front of the test section were built of wood, however. This material enabled the highest possible shape precision as well as cost-effective subsequent modifications. The newly designed nozzle made of wood features a hybrid design combining the conventional square shaped nozzle used in most wind tunnels and an aerodynamically optimised octagonal nozzle and capitalises on the advantages of both shapes.
At a glance
Participating institutes and centres:
- Centre for Aviation (ZAV)
- Centre for Product and Process Development (ZPP)
- Institute of Embedded Systems (InES)
Financing: ZHAW School of Engineering
Project status: completed