Experimental Studies on the Copper Refining Process
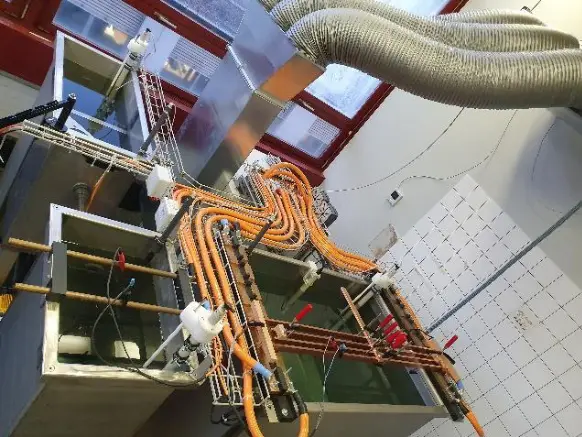
Hydrometallurgical raffination or copper electrolysis is the bottleneck of refining copper. Industrial copper electrolysis is still a relatively slow diffusion-based process, which can be accelerated by the selective use of forced convection. An experimental copper electrolysis facility has been developed to replicate and investigate said effects.
Copper electrolysis is used to refine blister copper from purity of around 98.5% up to 99.999%. Therefore, a cathode of pure copper is placed in a bath of electrolytes which consists of copper sulphate, sulphuric acid and some additional agents like glue and alcohol. The anode, usually made of blister copper, is placed parallel to the cathode.
During the process, a voltage of around 0.3V is applied between the cathode and the anode. As a consequence, the anode is dissolving. The copper ions follow the electric field to the cathode where they deposit. Impurities and more precious metals than copper sink to the ground where they can be collected as anode slime. Lower-grade metals stay in the solution. During the process, a second kinetic effect based on natural convection appears: The ion transport from the anode to the cathode changes the copper concentration in the electrolyte. Due to the resulting differences in density, the electrolyte sinks alongside the anode and rises alongside the cathode resulting in a circular flow field.
Industrial application of copper electrolysis is relatively slow. The kinetics of the ion transport process is based on natural convection and diffusion processes. Therefore, electrolysis is the bottleneck in the whole copper supply chain. Internal simulation-based pre-studies have shown that the existing electrolytic refining process can be significantly accelerated by the well-aimed intervention (forced convection) in the prevailing ion transport mechanisms between the electrode plates. Well-controlled, directed and constructive flow conditions can substantially support the slow, diffusion and natural convection-driven ion transport. Up to the present, this aspect has been considered only rudimentarily in the design of currently operating copper refining plants.
To investigate the behaviour of the developed flow devices a test stand that simulates the industrial electrolysis process was built. The process consists of two DC sources which produce the desired electrical voltages and currents. The copper electrolysis takes place in the large tank where anodes and cathodes are placed in parallel. During electrolysis, the electrolyte is increasingly contaminated and heated. A circulation pump transports the electrolyte from the electrolysis tank to the liberator where the amount of copper in the solution gets reduced. After the liberation, the electrolyte gets conditioned in the conditioner. In the conditioner the acidity is adjusted and, if necessary, base metals which are still dissolved in the electrolyte are pre-precipitated. If required a temperature management system will be implemented as well. After the conditioner, the electrolyte is returned to the electrolysis tank.